10 Days. 10 Stories. Part 3–2012
Edge computing ahead of its time. Challenge accepted. This brave new world of what we called 'secure data logistics' (more commonly referred today as 'Industrial Internet of Things') was extremely exciting. Instead of building rack cabinets of industrial PCs, switches & firewalls we put our efforts into designing a low power consumption (9-11 Watts!), small form factor networked appliance with our design partner Cogent Computer Systems Inc. From experience and customer feedback gained over the previous two years it made perfect sense to create a 100% passively cooled (fanless), ruggedized machine with enough processing power, memory & storage to run advanced software applications at remote sites.
So we introduced the ns-box…
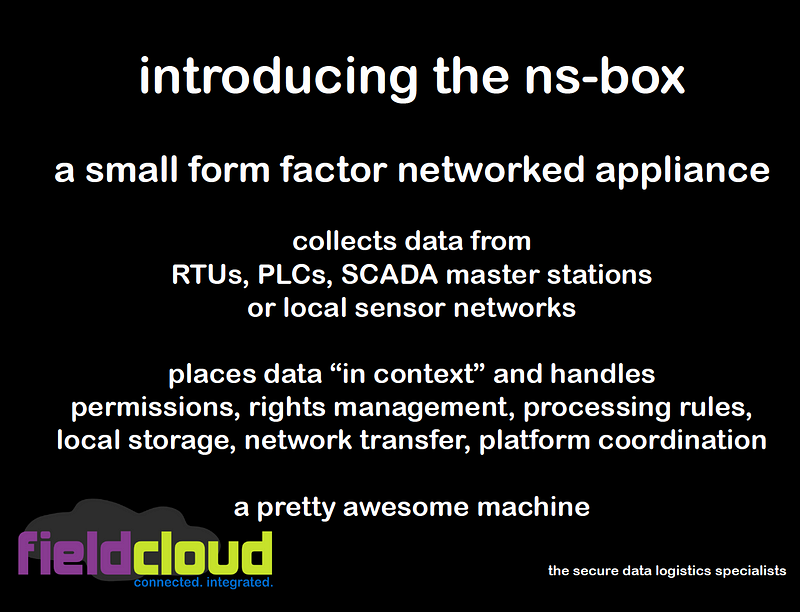
Our first prototype had a couple of flaws. We forgot to offset the Ethernet connectors to allow for the 2mm thick aluminium front plate so the final result looked a bit weird. While we were developing the gigabit Ethernet switch Linux device driver we discovered that the chip wasn't interfaced correctly to the CPU!
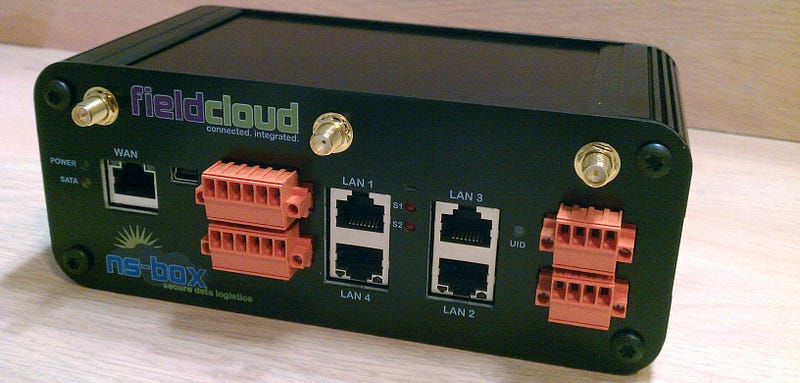
In Q1 2012 we did a PCB respin to correct the issues and also grew the board in size to make it easier to factory fit SIM cards. The other reason for growing the PCB was that we could use standard enclosure parts from our partner Lincoln Binns.
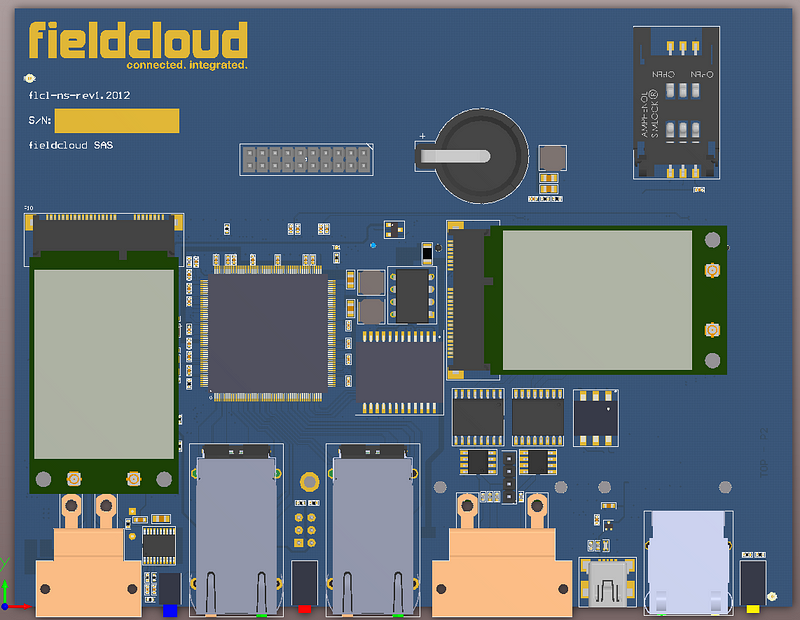
Building a custom Linux kernel and Debian operating system was a lot of fun. We wanted to keep the OS footprint as minimalist as possible while leveraging the vast collection of maintained software packages and libraries. This came in handy when we worked with clients on developing the end to end application stack and porting software from Intel PCs to our ARM9 platform.
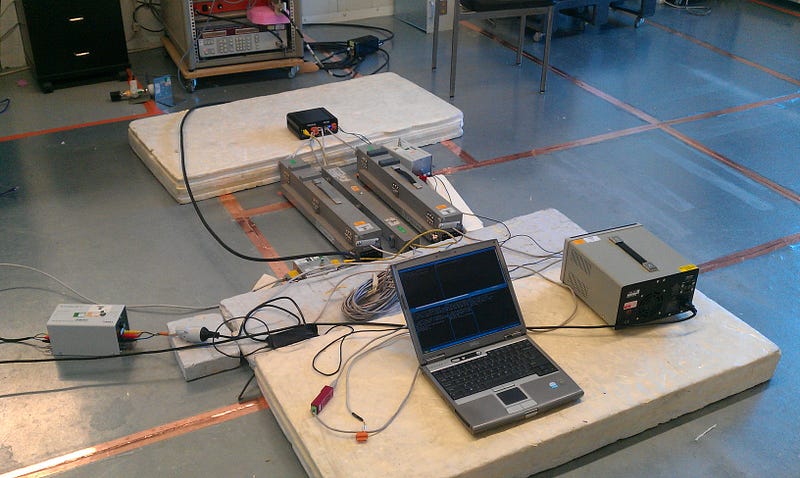
Of course, to bring the ns-box to market we had to take the product through formal laboratory testing at LCIE Bureau Veritas. This was another interesting learning experience and we are still grateful to the test engineers and their useful feedback which helped us improve the product further.
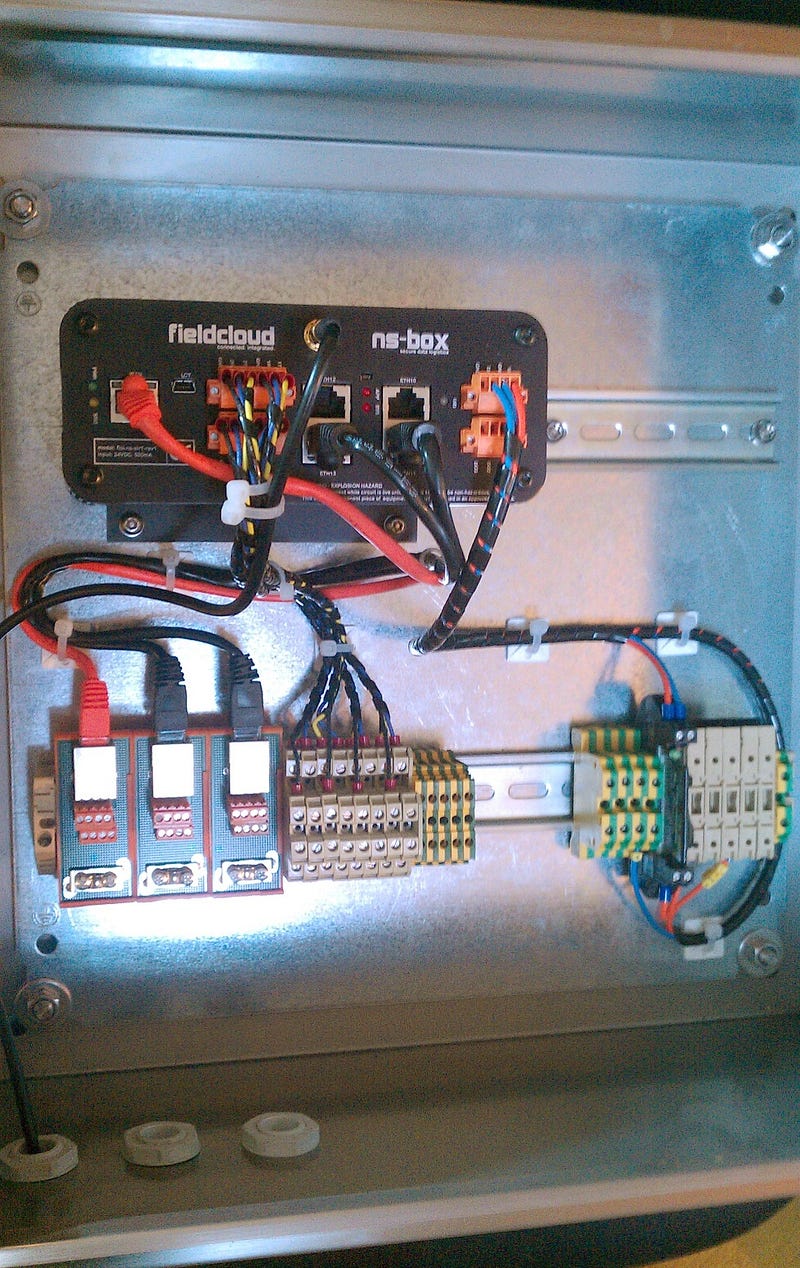
Of course, the ns-box was a component piece of equipment and had to be housed in a proper enclosure for deployment in harsh oil & gas production sites. We designed and built our own enclosures, offering a field-ready rapid deployment kit. These were first used in the United Arab Emirates for automating data delivery from downhole permanent gauge systems at remote well sites into the client's analytics applications hosted in their headquarters in Abu Dhabi.
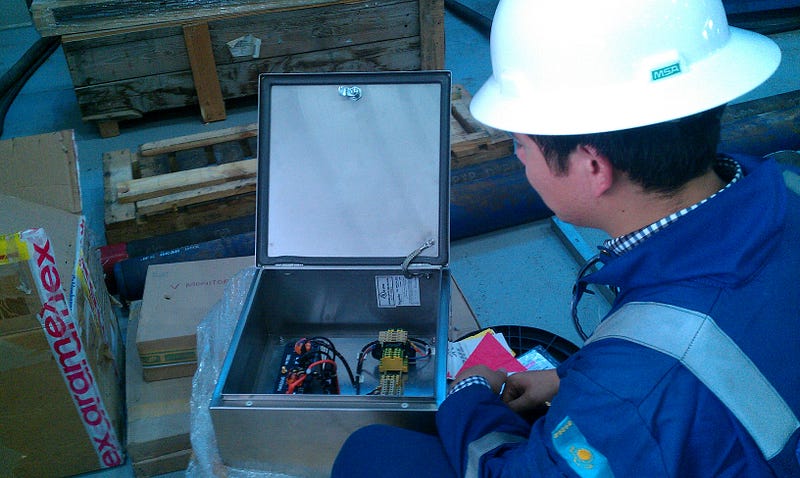
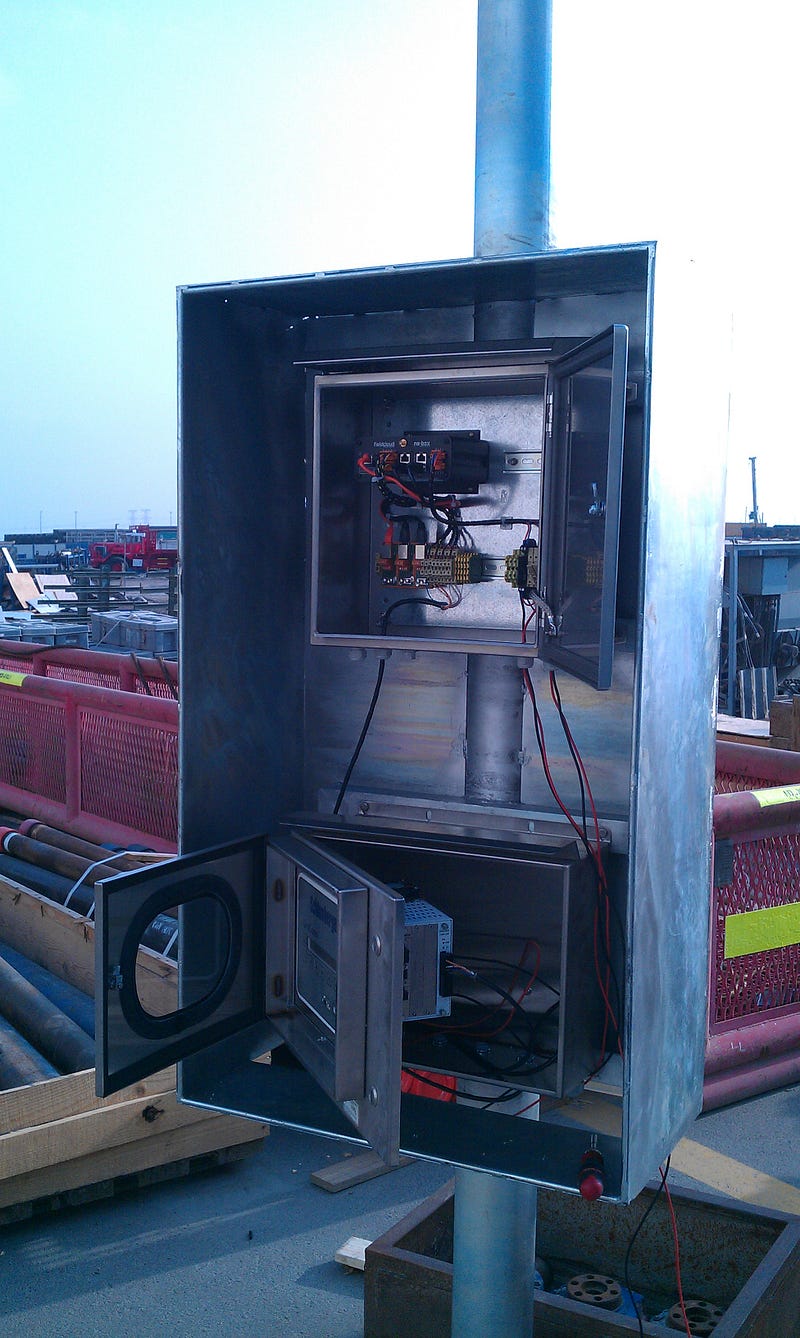
During our mission in Abu Dhabi we worked with a local contractor to built a mounting frame for deployment in at the client's desert location. This was going to be a totally self contained system, with solar power and cellular connectivity.
We finished 2012 on a high note, having successfully completed site integration testing and assembly for the client. Now it was time to prepare for the following year's adventures in desert.